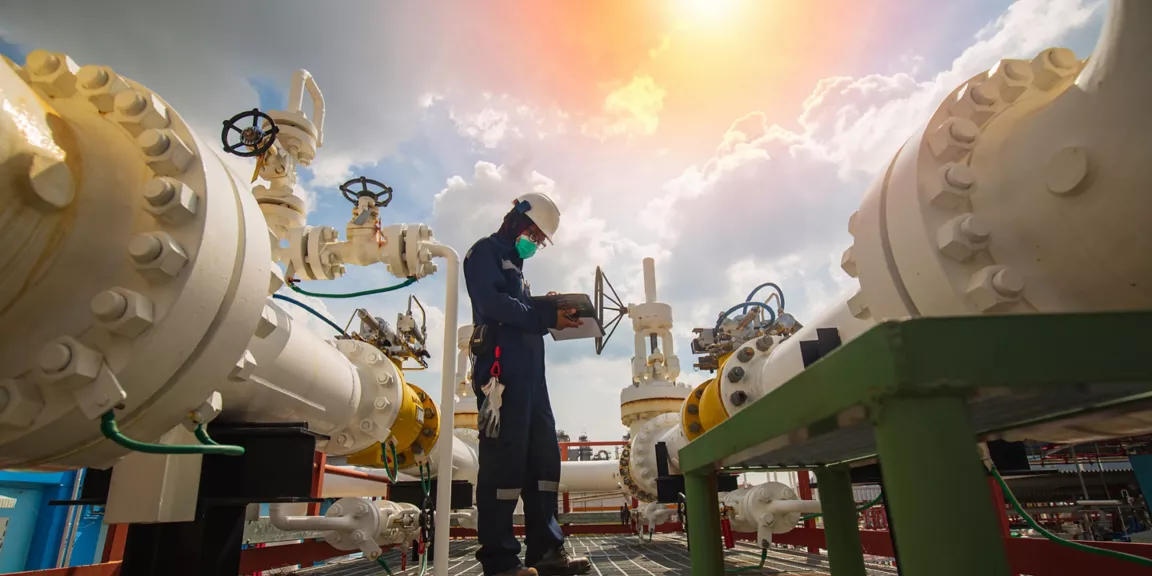
Unsafe industrial leaks trigger environmental damage, high financial costs, and safety dangers. A minor leak in water, steam, chemical, and gas systems, which stays unnoticed, poses significant risks through an extended timespan. Industrial leak detection represents a vital industrial process by allowing businesses to detect leakages, thus enabling them to perform needed repairs before system failure occurs.
A business operating without a leak detection plan becomes exposed to high expenses from system downtime alongside rising functional costs and regulatory violations. Hidden leaks create dangerous work conditions for employees because they elevate fire hazards and toxic emissions risks, possibly resulting in catastrophic explosions.
This blog will explore the importance of industrial leak detection, its benefits, and how organizations can implement a proper detection plan to enhance safety and cost savings.
The Effects of Industrial Leaks
Factors like aged infrastructure, equipment malfunction, corrosion, poor maintenance, and pressure cause industrial system leaks. The threats are variable based on the type of leak. However, every leak poses a potential hazard.
Let us consider various kinds of industrial leaks and their consequences.
Gas Leaks
Gas leaks are among the most dangerous because they can lead to asphyxiation, explosions, and fires. A small leak can be disastrous in industries that use gases like methane, hydrogen, or propane. Gas leaks can further contribute to environmental pollution, an increased carbon footprint for a company, and regulatory penalties.
Compressed Air and Steam Leaks
Steam and compressed air leaks are not ordinarily detectable as they often lack a detectable or odorous indicator. They are among the leading causes of energy waste in industrial plants. Leaky steam systems can lead to inefficient heating, increased energy costs, and equipment life reduction. Leaking compressed air similarly leads to pressure loss and makes air-powered equipment and tools less efficient, raising production costs.
Water and Fluids Leaks
Water or hydraulic system leaks lead to equipment failure, production downtime, and hazardous working conditions. Leaks in hydraulic fluid, in particular, are very slippery hazards, and water leaks can result in corrosion and electrical system damage. These leaks can lead to expensive repair and replacement if not addressed promptly.
Chemical Leaks
Industries that handle hazardous chemicals must prioritize detecting leaks to prevent environmental contamination, worker injuries, and legal responsibility. Leaks of chemicals can be dangerous since many chemicals are toxic or corrosive and have potentially severe health effects on workers and residents.
The Advantages of Industrial Leak Detection
Industrial leak detection makes workplaces safer, is cost-saving, and helps reduce operational inefficiencies. The most notable benefits of industrial leak detection are as follows:
Enhance Workplace Safety: Leak detection is critical to maintaining employee and equipment safety. Leak detection and early correction by companies can prevent accidents and reduce fire risks and exposure to toxic substances. A reliable leak detection system provides a safe working condition that enhances employee morale and productivity.
Substantial Cost Savings: Leaks are a waste of resources and lead to higher operational costs. Compressed air leaks can cost a plant thousands of dollars in wasted energy annually. Leaks in steam can lead to excessive fuel use and higher utility bills. Leaks that are addressed promptly can save firms a significant amount of money in the long run.
Product Quality and Efficiency Improvements: Leaks in process fluids can both degrade product quality and reduce yields. In food processing, pharmaceuticals, and manufacturing industries, fluid and gas system tightness ensures constant product quality. Leak detection helps optimize process conditions to improve overall efficiency and production.
Methods of Industrial Leak Detection
Many methods are used to detect and fix industrial leaks effectively. The most suitable technique depends on the type of system involved, the size of the leak, and industry regulatory needs.
The most common technologies used for leak detection are as follows:
Ultrasonic Leak Detection
Ultrasonic sensors identify leaks by picking up high-frequency sound waves released by escaping air or gas. This method is very effective for compressed air, gas, and steam leaks and allows technicians to quickly and effectively identify leaks.
Infrared (IR) Cameras
Infrared cameras identify temperature changes caused by leaks through thermal imaging. They efficiently find gas leaks in pipelines, steam systems, and electrical insulation failures.
Gas Detection Sensors
In hazardous gas handling industries, special gas detection sensors are required. These sensors continuously monitor air quality and trigger alarms when there are hazardous concentrations of gases.
Dye and Chemical Testing
Dye or tracer gas testing is often used in water, fuel, or refrigerant leak detection. A non-toxic tracer gas or a dye is introduced into the system and traced by UV light or a gas detector.
Acoustic Emission Testing
This sophisticated technique identifies leaks through the stress waves released by fluids that are escaping. It is typically applied in pipeline surveillance and significant industrial plants where visual inspections are not feasible.
Establishing an Effective Leak Detection Strategy
Companies must follow three key steps for effective leak detection, including scheduled inspections, advanced monitoring devices, and employee education programs. The following guideline reveals how organizations can build an effective leak-detection program:
Daily equipment checks enable teams to identify significant problems during their early stages. The scheduled maintenance program allows employees to discover and resolve leaks early.
Current leak detection devices on the market offer real-time monitoring capabilities alongside early alert systems, enabling businesses to react swiftly to developing issues. Extended investments in ultrasonic sensors, infrared cameras, and gas detection equipment greatly enhance detection system accuracy.
Learning programs for leak prevention enable employees to become key contributors in identifying leaks. Proper training about early warning indicators and detection instruments produces superior leak response outcomes.
A Leak Management Protocol should be established because it enables businesses to effectively guide their leak response, tracking, and execution procedures. An organized leak management procedure provides both leak documentation procedures alongside systematic procedures for addressing discovered leaks.
Implementing industrial leak detection mechanisms remains vital because they ensure operational security, reduce operational costs, and maintain efficiency. Protecting valuable assets, preserving life from dangerous gas leaks, and conserving steam and air compression energy are achievable through effective leak detection programs that ensure regulatory compliance. Business owners can minimize risks while improving productivity and minimizing costs through strategic investments in emerging leak detection systems and regular inspections supported by employee training programs. Take protective measures immediately since delaying could lead to expensive industrial failures.